Injection molding offers a high production rate for parts with precise dimensional tolerances. However, the cycle time for injection molding includes the cooling time as well as the clamping time to close and then open the mold.
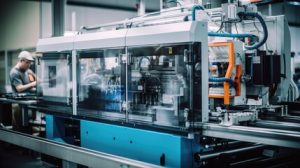
A molding consists of a sprue to introduce molten plastic and a runner to lead it to cavities that must be filled. Channels built into the mold also direct molten plastic to areas of the part that need to be strengthened. Contact Plastic Mold Injection Process Florida for more information.
Before production can begin, it’s essential to test the mold. This can reveal any issues like warping, incomplete fills, or surface imperfections, and allows the manufacturer to make adjustments before moving into full production. It might take some extra time, but it can prevent quality problems and costly rework down the road.
During this phase, the liquid plastic is heated to its melting point before it’s injected into the mold. The injection process itself is controlled by a number of factors, including temperature, pressure, and the injection speed. Depending on the type of plastic, these factors may be varied to achieve the desired end results.
Once the plastic is injected into the mold, it begins to cool and solidify. This cooling time can cause some shrinkage in the finished product, so the injection and molding processes must be carefully coordinated to minimize this effect.
The injection mold itself is designed with several channels that direct the flow of molten plastic into the various cavities to be formed. The molten plastic initially enters through a channel in the injection mold, known as the sprue bushing. From there, additional channels, called runners, carry the plastic to the cavity images. The sprue and runners must be carefully positioned to avoid any leakage and ensure the proper placement of the molded parts.
Once a runner has filled the required amount of material, it is closed off by a gate, which is also machined into the injection mold and sealed to prevent accidental opening. A portion of the melted plastic in the runners will solidify attached to the part during the cooling cycle and must be trimmed off. This scrap material can then be recycled by being reground into pellets. The reprocessed material can be used in place of virgin materials without negatively impacting the final product’s properties.
Once a good sample of the finished product is produced, it’s time to start making them in bulk. The first few pieces, referred to as T0 parts, will help the manufacturers fine-tune the mold and press settings. It’s important to ensure that all of the necessary adjustments are made before going into full production, because a single problem with the tooling can lead to poor-quality parts down the line.
Injection
The plastic injection molding process is used to create a number of products including kitchen and cooking items, office supplies and toys. It is also the method of choice when production needs are high and dimensional tolerances must be maintained. The ability to produce multiple identical and dimensionally consistent parts in quick succession makes this process ideal for high-volume production.
In the injection phase of the process, the two halves of the mold are closed by a clamping unit and held tightly while the material is injected. A hopper at the top of the injection machine receives raw plastic pellets and then feeds them into a barrel that contains a reciprocating screw. The heating and cooling of the screw – which can be driven hydraulically or by steam pressure – serves to melt the plastic pellets into a molten state.
From there, the molten plastic is conveyed to the front of the mold through a system called a runner and into each cavity through a gate. A sprue (the opening feed that conveys the molten plastic from the injection machine to the runner system) and a series of gates regulate the flow of the melted plastic into each cavity.
Once the molten plastic fills each cavity to a point that is 95%-99% full, it enters a holding stage during which injection pressure is replaced by a holding pressure. This ensures that the molten plastic stays compacted during its cooling phase. The temperature of the molded plastic and the speed at which it cools should be controlled to avoid defects such as blistering, shrinkage or warping.
As the molded plastic cools, a system within the mold helps it release its heat by transferring it to a coolant. The molded part will often shrink during this process, so additional melted plastic is added to compensate.
Once the molded part has sufficiently cooled, it is ejected from the mold. The mold is then reopened and the cycle begins again. The plastic injection molding process relies on the rapid heating and cooling of the molten plastic to form its shape. Therefore, it is important to choose a mold design that allows the plastic to solidify in an even manner. This can be accomplished by using wall thickness that is uniform and avoiding areas that may be subject to pressure changes during the manufacturing process.
Cooling
After a period of time in which the plastic has been molded, it begins to cool and solidify. This is a crucial step, since it allows the plastic to transition from its liquid state to a solid state and naturally shrinks as it does so. This cooling process is also a key factor in determining part quality, as it directly affects the strength, dimensional accuracy, and surface finish of the finished product.
The amount of time that the plastic takes to properly cool is a function of both the thickness of the part and the type of plastic used. Generally, thin sections of the plastic cool faster than thicker ones. Injection molds are designed with cooling channels to circulate coolant, such as water, around the injection mold to absorb and remove heat from the molten plastic. The design of these channels must be carefully analyzed to ensure that the mold can maintain a proper temperature throughout the cooling process.
If the cooling channels are poorly placed, the plastic may not be able to cool evenly. This could lead to warping or other defects in the finished product. Often, the problem can be resolved by adding features to the injection mold that help produce a more turbulent flow of the coolant. These features, called bafflers and bubblers, are fitted into drilled or milled holes in the injection mold. They help create a more efficient cooling circuit by introducing turbulence that allows the coolant to absorb and remove heat from the injection mold more effectively.
Another way to improve the cooling of the injected plastic is by reducing its cycle time, which is the amount of time it takes for the injection molding machine to move from the pack and hold stage to the ejection stage. By reducing the cycle time, engineers can produce more parts in less time and still ensure that the finished products meet or exceed quality standards. This is accomplished by evaluating the complexity and efficiency of the cooling channels, as well as the injection mold’s geometry and construction. Depending on the type of plastic and the mold design, this evaluation can be performed by utilizing simulation software or referring to standard guidelines.
Ejection
The plastic injection molding process must incorporate an ejection system that will properly and safely eject the finished part from the mold. A poorly designed ejection system can damage the product, or result in a defective or incomplete part. The type of ejection system chosen depends on the geometry of the molded product, the material being used, and the production rate desired.
One of the most common types of ejection systems is the use of a series of pins that are fitted into the base plate of the mold inside predesigned indentations. The pins then eject the molded product by pushing against it with enough force to break the seal created between the part and the mold. This ejection system is inexpensive and efficient, but it can leave visible marks on the molded product.
Another method of ejection is through a pneumatic ejector plate system, which uses air pressure to operate a series of ejector plates that push the molded product out of the mold. This system is a good choice for products that require moderate ejection force and take into account spatial constraints. It also provides fast ejection, making it a good choice for high-production applications.
To improve the ejection of the molded product, manufacturers may include design features in the tooling that can be implemented during the injection phase. These include assigning parting lines, removing undercuts, and adding draft angles. By addressing these design issues, the plastic engineer can help to ensure that the molded product will eject correctly when the mold opens.
Once the product has cooled, it is ready to be ejected from the mold. The ejection phase must be completed in a timely manner, so that the molded product can be removed from the injection machine for assembly and packaging. In addition, the ejection phase should leave the injection mold in a clean and ready-to-use condition for the next cycle. If the mold is not cleaned and purged in time for the next cycle, it may cause an undesired warping of the plastic or the formation of defects such as blisters on the surface of the finished part.